.jpeg)
Maximize Your Fleet Uptime with Proactive Maintenance!
Maximize your fleet uptime with proactive maintenance strategies from B&B Truck & Trailer Repair in Colona, IL. Save on downtime and repairs by staying ahead of issues.
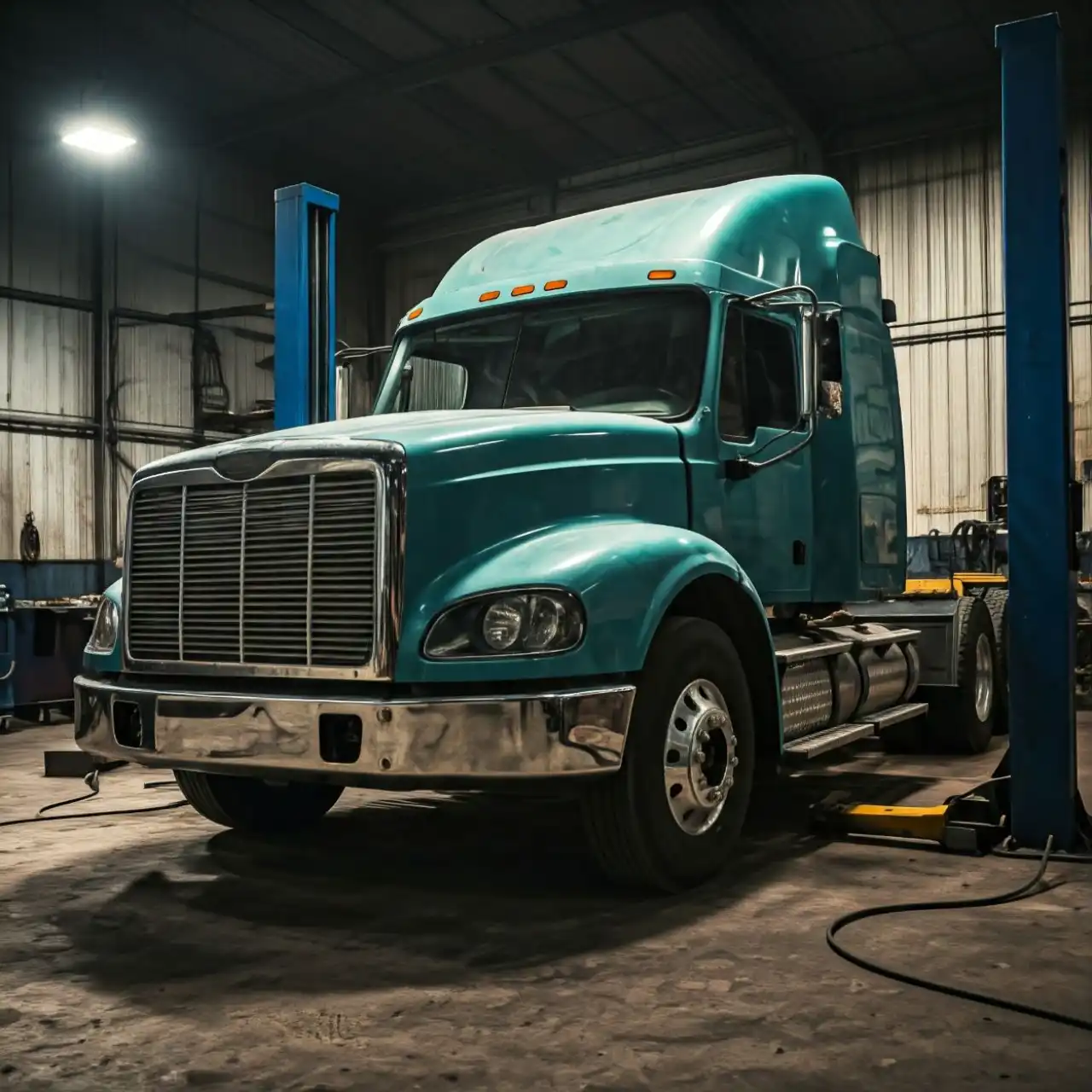
It’s difficult to balance the maintenance of heavy-duty trucks and fleet hauls when uptime is everything. Every minute your trucks spend off the road translates into missed deliveries, unhappy clients, and lost revenue. However, many fleet operators wait until a breakdown happens before taking action. This is not just costly but also avoidable. Enter proactive maintenance, a strategy that maximizes your fleet’s uptime by preventing issues before they snowball into expensive problems.
Let’s take a closer look at how proactive maintenance can be a game changer for your fleet and how you can implement it for your trucks.
The Importance of Proactive Maintenance for Fleet Uptime
When you run a fleet of trucks, keeping your rigs on the road is the highest priority. But, waiting for things to go wrong (reactive maintenance) is a costly way to operate. Unplanned repairs, roadside breakdowns, and emergency parts replacements can impact your operational budget.
Proactive preventive maintenance focuses on identifying and fixing potential problems before they lead to downtime. By scheduling regular inspections and repairs based on manufacturer recommendations and actual truck data, fleet managers can save money and ensure their trucks spend more time on the road and less time in the shop.
Key Components of Proactive Maintenance
So, what does proactive maintenance entail for a heavy-duty truck fleet? Here are some of the critical areas to focus on:
1. Scheduled Inspections
One of the easiest ways to prevent costly breakdowns is by adhering to a scheduled inspection routine. Most manufacturers provide maintenance schedules based on time, mileage, or engine hours. Following these guidelines ensures that critical systems like the engine, transmission, and brakes are inspected and serviced regularly. You can set up a digital maintenance schedule for each truck in your fleet, to track mileage, engine hours, and service records to ensure nothing is missed.
2. Oil and Fluid Analysis
Engine oil, transmission fluid, differential oils, and power steering fluid and coolant all play a vital role in keeping your truck running smoothly. Performing oil and fluid analysis can help you detect potential issues, such as contaminants, that signal internal wear or failing seals. Consider a fluid analysis every 15,000 miles to catch wear-related problems early and extend the life of your components.
3. Tire Maintenance
Tires are one of the most important and often overlooked parts of your truck. Proper tire maintenance ensures better fuel efficiency, improved handling, and safety on the road. Regularly check for tread wear, proper inflation, and signs of damage. It’s best to rotate your tires every 10,000 miles and keep them inflated to the manufacturer’s recommendations for better wear and fuel economy. Tire rotations every few months ensure that your tires have even wear, increasing overall fleet efficiency.
4. Fuel System Care
For diesel engines, maintaining a clean and efficient fuel system is critical. This means changing fuel filters regularly and using fuel additives to keep injectors clean. A clogged fuel system can lead to loss of power, increased fuel consumption, and even engine damage. Clean your fuel injectors and replace the fuel filter every 15,000 miles to keep your trucks running efficiently.
5. Battery and Electrical System Checks
Batteries are a critical part of your truck’s starting system and electrical components. Keeping tabs on battery health and ensuring connections are corrosion-free can prevent unexpected power failures. Test the battery at every oil change to ensure it's holding charge properly. Clean terminals to avoid corrosion buildup and inspect alternators as they are essential for your truck’s electrical systems.
How to Implement a Proactive Maintenance Program
Starting a proactive maintenance program may seem daunting, but it doesn’t have to be. Here are a few key steps to get you going:
Create a Maintenance Schedule: Work with your team to develop a maintenance schedule based on manufacturer recommendations and your specific fleet's usage patterns. This should include daily inspections by drivers, weekly and monthly checkups, and annual comprehensive inspections.
Train Your Drivers: Drivers are your first line of defense when it comes to spotting potential issues. Make sure they know how to perform daily inspections, check for early signs of problems, and communicate with the maintenance team.
Use Fleet Management Software: Fleet management software can track your vehicles' maintenance needs, keep records of past services, and alert you when it’s time for the next check-up. This takes the guesswork out of proactive maintenance.
Partner with a Reliable Service Provider: Find a trusted fleet maintenance partner who can help carry out the necessary inspections and repairs. A good partner will understand the needs of your fleet and help you maximize uptime.
Benefits of Proactive Maintenance
Reduced Downtime: The most significant benefit of proactive maintenance is the reduction of unexpected downtime. Instead of waiting for something to break, you’re addressing issues when it’s convenient—during a scheduled stop.
Extended Vehicle Lifespan: Regular maintenance—like oil changes, fuel system cleaning, and tire rotations—can significantly extend the lifespan of your vehicles. Well-maintained trucks experience fewer breakdowns and perform better over time.
Lower Repair Costs: Proactive maintenance addresses small issues like worn brake drums leading to cheaper services than replacing an entire brake system after a failure. The same goes for other components of truck systems like engines, transmissions, or drivelines—cleaning and repairing individual parts regularly costs a fraction of what it takes to replace entire system failures.
Improved Fuel Efficiency: Trucks that are well-maintained operate more efficiently. When fuel filters, air filters, and tire pressures are kept in check, the engine doesn’t have to work as hard, leading to better fuel economy. In a fleet, even minor improvements in fuel efficiency can result in significant savings.
Increased Safety: Proactive maintenance also keeps your drivers and others on the road safer. Well-maintained trucks are less likely to experience critical failures like brake or tire blowouts. By keeping up with safety inspections, you ensure your fleet is operating at its best and reduce the risk of accidents.
Proactive Maintenance With Optimal Fleet Management
At the end of the day, proactive maintenance is the key to maximizing your fleet's uptime. With regular inspections and fluid analysis, you can catch small problems before they turn into big ones. Not only will this keep your trucks on the road, but it will also save you money in the long run.
Looking to implement a proactive maintenance program for your fleet? Reach out to B&B Truck & Trailer Repair in Colona, IL for expert advice and service. We’ll help keep your fleet running at peak performance and minimize downtime. If you want to learn more about the industry, give our article on mobile truck repairs a read.
More Articles
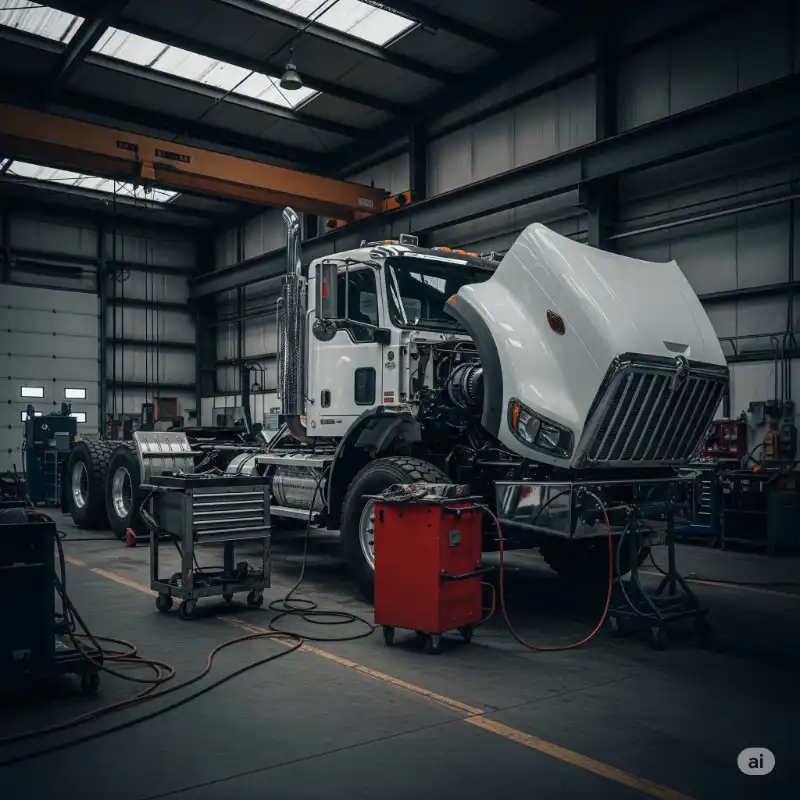
Common Fleet Maintenance Errors That Cause Unnecessary Downtime
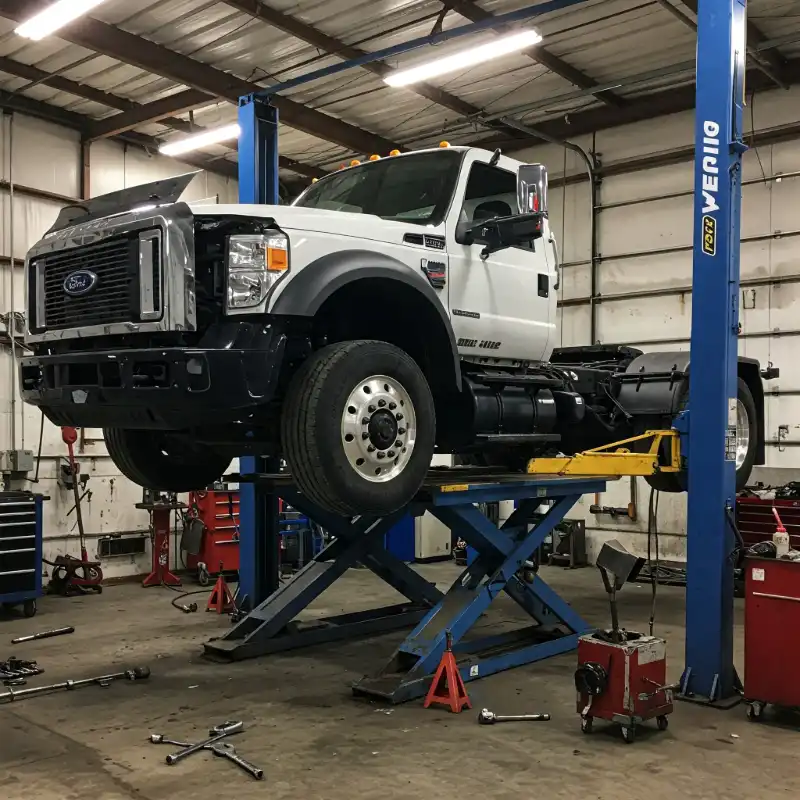
Why Is Regular Trailer Maintenance Critical for Safety?
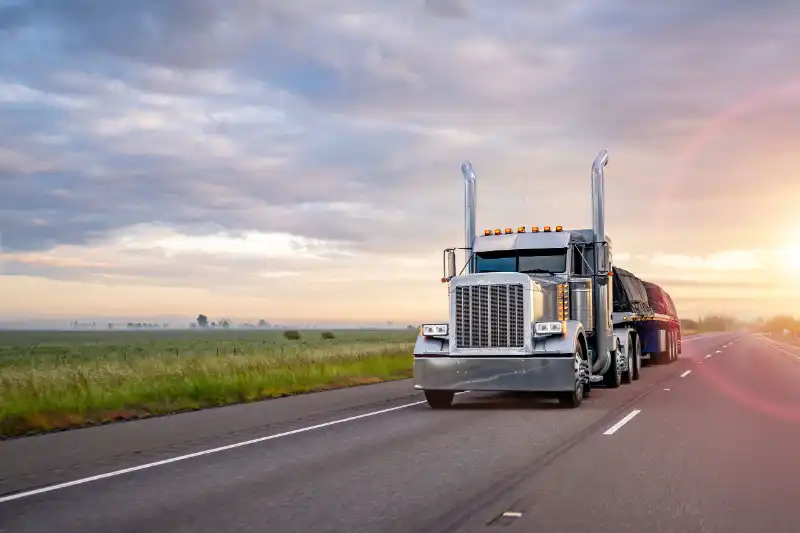
Why Is Regular Fleet Maintenance Crucial for Business Success?
Contact Us
Visit our full-service truck & trailer repair shop in Colona, Illinois, or take advantage of our mobile services offered throughout the Quad Cities area, including Moline & Rock Island, IL & Davenport & Bettendorf, IA. Give us a call, drop by the shop, or fill out our service request form!
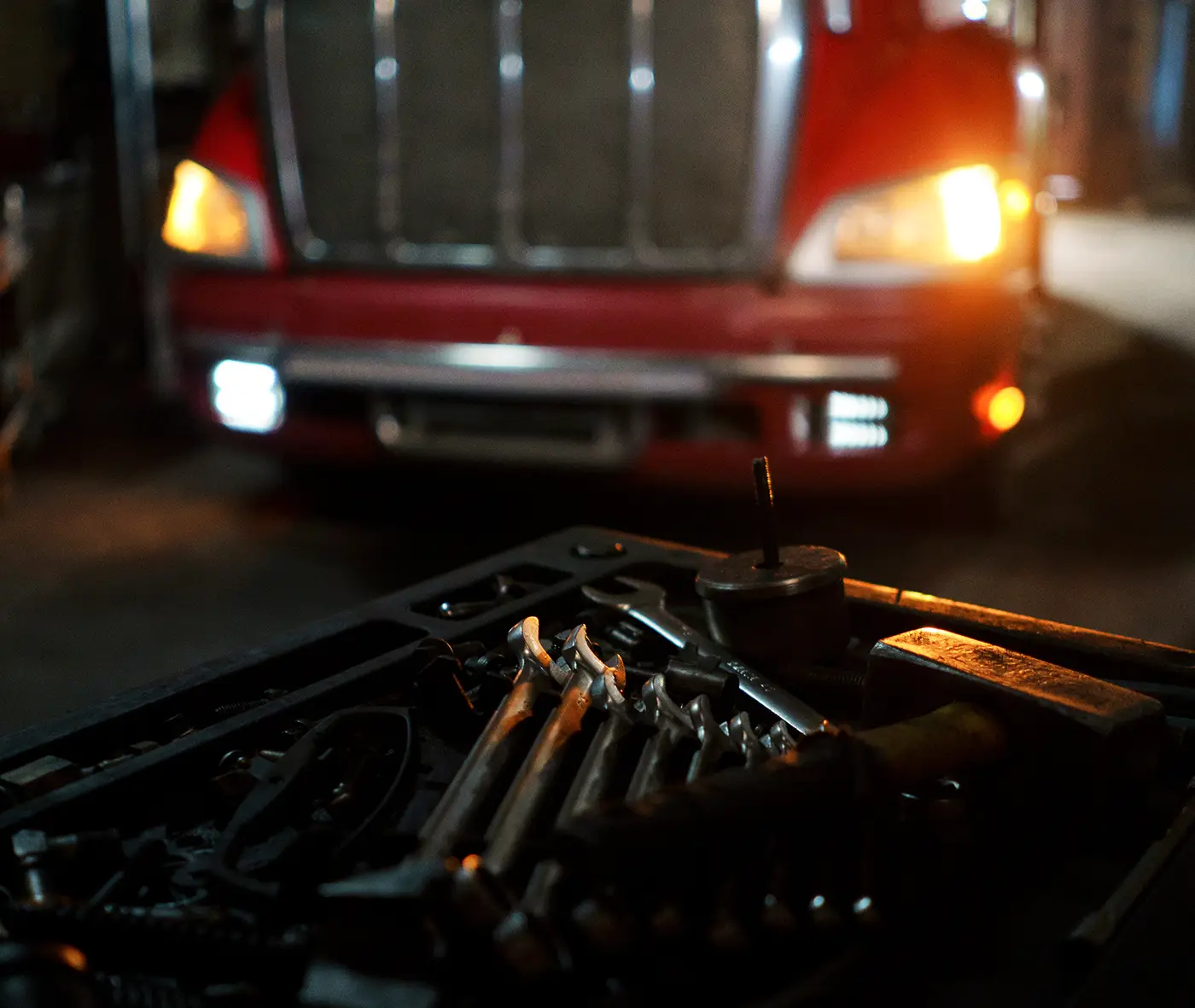